- Blog
- Research and Engineering
- Opening the Orb: A look inside Worldcoin’s biometric imaging device
Opening the Orb:
A look inside Worldcoin’s biometric imaging device
Given the scope of Worldcoin’s mission, we approach everything from a set of founding principles based on privacy, trust and transparency.
That’s why we remain committed to open sourcing as much of the technology we create and use as possible. We also want to enable others to develop, build and operate similar devices that integrate with the World ID protocol, with the ultimate goal of fully decentralizing every part of the project.
The intention of this post is to share specific, substantive details about the hardware we’re building. After three years of R&D, we’re excited to showcase the Orb, explain at a high level how it works and release corresponding hardware engineering files. We see this as an important step on our journey to making our commitment to transparency more credible to the global community.
Over the coming months, we’ll publish more articles explaining other parts of the Orb and the sign-up flow.
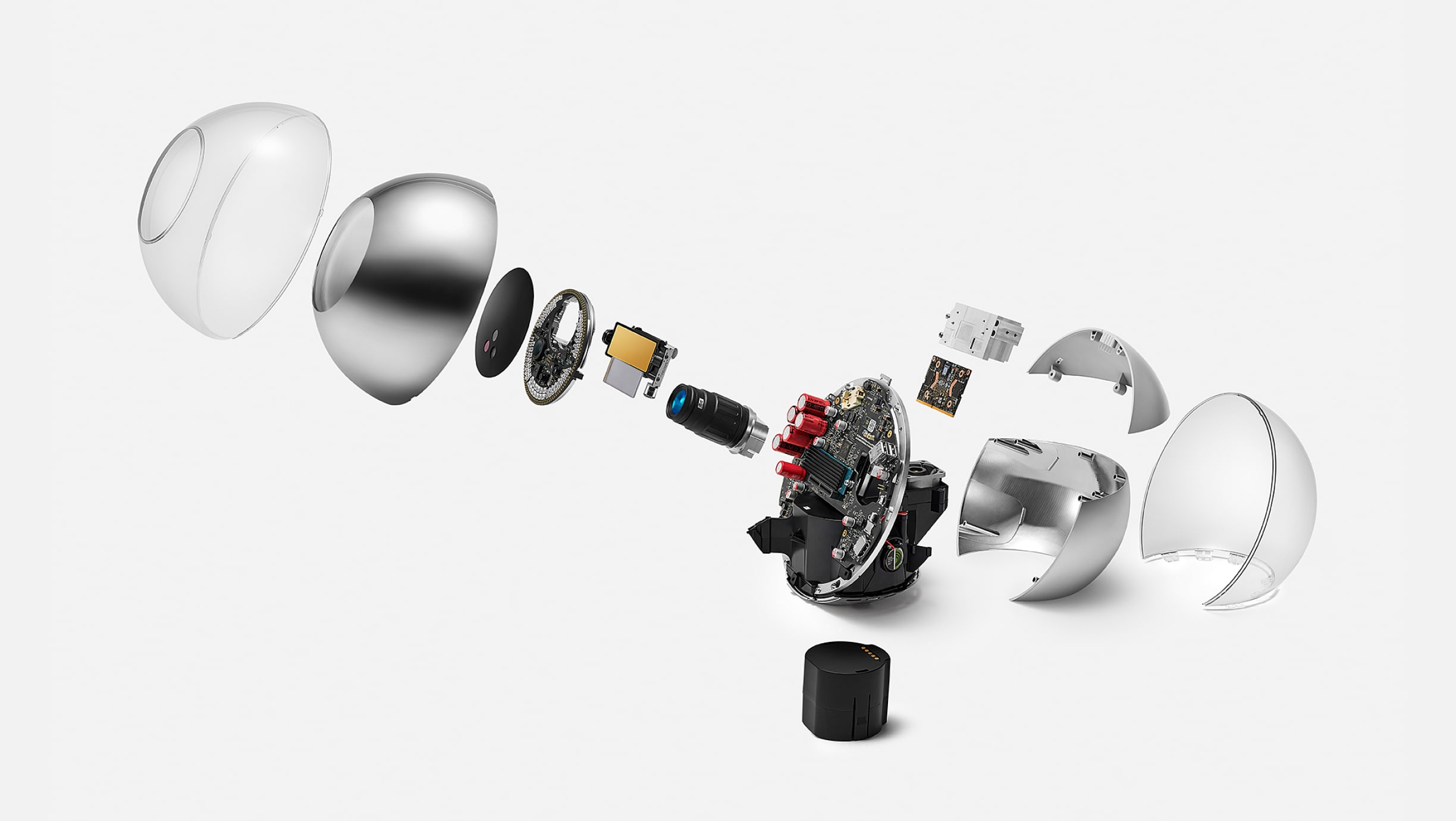
Why did we need custom hardware,
and why does it scan the iris?
When Worldcoin started, we didn’t intend to develop a physical device, let alone one built for biometric imaging. Building custom hardware is difficult and expensive, and no one wants to do it if they can avoid it. Instead, our goal was to freely distribute a new digital token to everyone in the world as a way to help them access and participate in the global economy. It was only after concluding that biometrics are the sole realistic way of achieving our goal that we set out to create the Orb.
Learn more about the inclusivity of biometrics and why Worldcoin uses them here.
As we explored many different ways to solve sybil resistance and prove unique personhood, our research showed that iris scanning offers the most accurate biometrics with an acceptable user experience that has been successfully tested at scale. This is because the iris has strong fraud resistance and data richness, meaning it can be used to accurately differentiate between billions of unique humans. The more data rich the biometric marker (e.g., the iris), the fairer and more inclusive the system.
Importantly, false rejections are not constant but increase with scale. Eventually, most systems hit a wall and do not allow anyone new to join. This means that existing technologies with less data richness like FaceID would only be able to accommodate a few million people.
Since commercially available iris imaging devices did not meet our technology or security needs, we spent years developing our own to enable universal access to the global economy in the most inclusive manner possible. More details can be found here.
The Orb hardware repository
As a first step towards open sourcing the Orb, we’re releasing all relevant, hardware-related engineering files for its current version in our repository. You can download Eagle (PCBs) to view the files and use Autodesk’s CAD viewers for free. Feedback for design improvements is welcome and highly encouraged.
We’re aware that, by developing the Orb, we’re advancing state-of-the-art iris biometrics. That’s why all files are published under a license that’s based on the MIT license but prohibits the use of the licensed materials for surveillance applications as well as any other applications that could be harmful to the rights of individuals.
The remainder of the article will go through a teardown of the Orb, with a few engineering anecdotes included.
The Orb teardown
Three years of R&D, including one year of small-scale field testing and one year of transition to manufacturing at scale, have led to the current version of the Orb.
Today’s Orb represents a precise balance of development speed, compactness, user experience, cost and at-scale production with minimal compromise being made on imaging quality and security. There will likely be future versions that are optimized even further. However, the current version represents a key milestone that allows us to increase the number of Orbs in the field.
We’ll now take you through some of the most important engineering details of the Orb, as well as how the imaging system works. For security purposes, we will only explicitly leave out tamper detection mechanisms that are meant to catch intrusion attempts.
Removing the Shell
When removing the shell, the mainboard, optical system and cooling system become visible. Most of the optical system is hidden in an enclosure that, together with the shell, forms a dust- and water-resistant environment to enable long-term use even in challenging environments.
What you see is a device that has been refined through multiple prototype and design for manufacturing (DFM) iterations.

Fig. 1
Orb underneath the shell
The Orb consists of two hemispheres separated by the mainboard which is tilted at 23.5°—the angle of the rotational axis of the earth. The mainboard holds a powerful computing unit to enable local processing for maximum privacy. The frontal half of the Orb is dedicated to the sealed optical system. The optical system consists of several multispectral sensors to verify liveness and a 2D gimbal-enabled narrow field of view camera to capture high resolution iris images. The other hemisphere is dedicated to the cooling system as well as speakers. An exchangeable battery can be inserted from the bottom to enable uninterrupted operation in a mobile setting.
Mechanics
Once the shell is removed, the Orb can be divided into four core parts:
- Front: The optical system
- Middle: The mainboard separates the device into two hemispheres (note: its inclination is exactly 23.5°, equivalent to the inclination of the rotational axis of the earth)
- Back: The main computing unit as well as the active cooling system
- Bottom: An exchangeable battery

Fig. 2
Explosion CAD of all relevant components
With the housing material removed (e.g. the dust-proof enclosure of the optical system), all relevant components of the Orb become visible. This includes the custom lens, which is optimized for both near infrared imaging and fast, durable autofocus. The front of the optical system is sealed by an optical filter to keep dust out and minimize noise from the visible spectrum to optimize image quality. In the back, a plastic component in the otherwise chrome shell allows for optimized antenna placement. The chrome shell is covered by a clear shell to avoid deterioration of the coating over time.
We field tested our first prototypes outside the lab as early as possible. Naturally, this taught us many lessons, including:
Optical System
With the first prototype, the signup experience was notoriously difficult. Over the course of a year we upgraded the optical system with autofocus and eye tracking such that alignment becomes trivial when the person is within an arm's length of the Orb.
Battery
No battery we tried would last for a full day on a single charge. So we built a custom exchangeable battery based on 18650 Li-Ion cells—the same form factor as the cells used in a Tesla Model S. The battery consists of 8 cells with 3.7V nominal voltage in a 4S2P configuration (14.8V) with a capacity of close to 100Wh, which is a limit imposed by regulations related to logistics. Now there’s no limit to Orb uptime.

Fig. 3
Custom exchangeable battery
The Orb’s custom battery is made of Li-Ion 18650 cells (the same cells used in many electric cars). With close to 100Wh, the capacity is optimized for battery lifetime while complying with transportation regulations. A USB-C connector makes recharging convenient.
Shell
The coating of the shell sometimes deteriorated in the handheld use case. Therefore, we added a 2mm clear shell to both optimize visuals as well as protect the chrome coating from scratches and other wear.
UX LEDs
To make the user experience more intuitive, especially in loud environments where a person might not be able to hear sound feedback, we added an LED ring to help guide people through the sign-up process. Similarly, we exposed status LEDs next to the only button on the Orb to indicate its current state.
How the Optical System Works
Our early field tests taught us that the verification experience needed to be even simpler than we had anticipated.
To do this, we first experimented with many approaches featuring mirrors that allowed people to use their reflection to align with the Orbs imaging system. However, designs that worked well in the lab quickly broke down in the real world.
We ended up building a two-camera system featuring a wide angle camera and a telephoto camera with an adjustable ~5° field of view by means of a 2D gimbal. This increased the spatial volume in which a signup can be successfully completed by several orders of magnitude, from a tiny box of 20x10x5mm for each eye to a large cone.

Fig. 4
Telephoto lens and 2D gimbal
The main imaging system of the Orb consists of a telephoto lens and 2D gimbal mirror system, a global shutter camera sensor and an optical filter. The movable mirror increases the field of view of the camera system by more than two orders of magnitude. The optical unit is sealed by a black, visible spectrum filter which seals the high precision optics from dust and only transmits near infrared light. The image capture process is controlled by several neural networks.
The wide angle camera captures the scene, and a neural network predicts the location of both eyes. Through geometrical inference, we steer the field of view of the telephoto camera to the location of an eye to capture a high resolution image of the iris, which is further processed by the Orb into a unique identifier.
Learn more about our commitment to privacy here.
Beyond simplicity, the image quality was the main focus. We tested many off-the-shelf products but didn’t find a compact-enough lens that met our imaging requirements while still being affordable. Therefore, we partnered with a well known specialist in the machine vision industry to build a customized lens.
The lens is optimized for the near infrared spectrum and has an integrated custom liquid lens which allows for neural network controlled millisecond-autofocus. It is paired with a global shutter sensor to capture high resolution, distortion free images.

Fig. 5, a)
Custom telephoto lens
The telephoto lens was custom designed for the Orb. The glass is coated to optimize image capture in the near infrared spectrum. An integrated liquid lens allows for durable millisecond autofocus. The position of the liquid lens is controlled by a neural network to optimize focus. To capture images free of motion blur, the global shutter sensor is synchronized with pulsed illumination.
b) A comparison of the image quality of the Worldcoin Orb vs. the industry standard clearly show the advancements we’ve made in the space
The camera and the corresponding pulsed infrared illumination are synchronized to minimize motion blur and suppress the influence of sunlight. This way, the Orb creates lab environment conditions for imaging, no matter its location. Needless to say, the infrared illumination is compliant with eye safe standards (such as EN 62471:2008).
Image quality was the one thing we never compromised no matter how difficult it was. In terms of resolution the Orb is orders of magnitude above the industry standard. This provides the basis for the lowest error rates possible to, in turn, maximize the inclusivity of the system.
Electronics
When disassembling the Orb further, you’ll find several PCBs (Printed Circuit Boards), including the front PCB containing all illumination, the security PCB for intrusion detection and the bridge PCB which connects the front PCB with the largest PCB: the mainboard.

Fig. 6
The front of the mainboard
The front of the mainboard holds capacitors to power the pulsed, near infrared illumination (certified eye safe). There are also drivers to power the deformation of the liquid lens in the optical system. A microcontroller controls precise timing of the peripherals. An encrypted M.2 SSD can be used to store images for voluntary data custody and image data collection. Those images are secured by a second layer of irreversible encryption via the public key from a server such that, in the unlikely event of a compromised Orb, no data would be exposed. The contribution of data is optional and data deletion can be requested at any point in time through the app. A SIM card slot enables optional LTE connectivity.

Fig. 7
The back of the mainboard
The back of the mainboard holds several connectors for active elements of the optical system. Additionally, a GPS module enables precise location of Orbs for fraud prevention purposes. A Wi-Fi Module equips the Orb with the possibility to upload iris codes to make sure every person can only sign up once. Finally, the mainboard hosts a Nvidia Jetson Xavier NX which runs multiple neural networks in real time to optimize image capture, perform local anti-spoof detection and calculate the iris code locally to maximize privacy.
The mainboard acts as a custom carrier board for the Nvidia Jetson Xavier NX SoM powering the Orb. Apart from the Jetson, the other major “plugged-in” component is a 250GB M.2 SSD. The SSD can be used to buffer images for voluntary data custody and image data collection. Images are irreversibly encrypted with a public key from the server such that, in the unlikely event of a compromised Orb, no data would be exposed. The contribution of data is optional and data deletion can be requested at any point in time through the app.
Further, a STM32 microcontroller controls time-critical peripherals, sequences power, and boots the Jetson. The Orb is equipped with Wi-Fi 6 and optional LTE to enable seamless connectivity as well as a GPS module to locate the Orb and prevent misuse. Finally, a 12 bit liquid lens driver allows for controlling the focus of the telephoto lens with a precision of 0.4mm.
The most densely packed PCB of the Orb is the front PCB. It mainly consists of LEDs. The outermost RGB LEDs power the “UX LED ring.” Further inside, there are 79 near infrared LEDs of different wavelengths. The Orb uses 740nm, 850nm and 940nm LEDs to capture a multispectral image of the iris to make the uniqueness algorithm more accurate and detect fraud.

Fig. 8
Front PCB with near infrared illumination
The front PCB powers multispectral illumination as well as fraud prevention sensors. Bright illumination (which is certified eye safe) is needed for high quality image capture, like in a photography studio. Fraud prevention algorithms based on the multispectral sensors are designed to prevent spoofing and run locally on the Orb for maximum privacy. No data from those images is uploaded unless specifically requested by a person. Circular LEDs in the visible spectrum at the border of the PCB enable precise user feedback.
The front PCB also hosts several multispectral imaging sensors. The most basic one is the wide angle camera, which is used for steering the telephoto iris camera. Since we’re giving away a free share of Worldcoin to every person who chooses to sign up through the Orb, the incentives for fraud are high. Therefore, we included further imaging sensors for fraud prevention purposes.
When designing the fraud prevention system, we started from first principle reasoning: which measurable features do humans have? From there, we experimented with many different sensors and eventually converged to a set that includes a near infrared wide angle camera, a 3D time of flight camera and a thermal camera. The system was designed to enable maximum privacy, so the fraud prevention algorithms based on the input from those sensors run locally. No images ever leave the device unless a person explicitly requests to back up their data for future upgrades and agrees to help us improve the system for everyone.
What’s next
In this post, we revealed and explained many of the most important components of the Orb and linked to the corresponding engineering files. We see this as an important step towards demonstrating our commitment to privacy, trust and transparency. As stated at the outset, we are dedicated to open sourcing as much of our technology as possible and ultimately fully decentralizing the project.
Manufacturing of the latest generation of Orbs is already well underway in Germany, as well as their distribution to new Worldcoin Operators in cities around the world. In fact, they’ve already helped Worldcoin pass more than one million sign-ups—an important milestone on the way to providing universal access to the global economy.
Explanatory Note: Tools for Humanity (TFH) led the initial research and development of the Worldcoin protocol, including the Orb. This year, prior to the launch of the decentralized network, the non-profit Worldcoin Foundation is taking over responsibility for facilitating participation in, and the continued development of, the protocol. The Worldcoin Foundation will continue to support and grow the Worldcoin community until it becomes self-sufficient, while TFH will support the Foundation, including by manufacturing and shipping Orbs. Currently in beta, Worldcoin expects to launch in the first half of 2023.